heater racks& subassemblies
Improve cure timeS, Save space & reduce operating costs
Catalytic Industrial Systems gas catalytic heaters burn gas at significantly lower temperature than traditional gas heaters, which means consistent & even heat distribution. Heaters on Racks are designed and built to meet specific application demands and are suitable for retrofit or custom enclosures for preheating, drying, powder gelling, boosting, curing and more. Multiple heater sizes allow for flexible configurations that can process virtually any shape or size of product to be cured.
Racks are assembled at CIS factory with electrical and gas plumbing terminated at a common point at each rack to reduce onsite work for a quicker startup. The racks are controlled with a PLC and HMI with Ethernet interface capabilities. The control system can be configured to operate the racks in either vertical or horizontal zones to ensure the most efficient heat coverage and distribution. CIS engineering team will design a system to generate the precise energy distribution and achieve a uniform cure for all of the components you process.
Mobile dry racks (MDR)
Mobile Dry racks are designed to offer maximum flexibility and mobility. The support structure of the Mobile Dryer Racks offers adjustability in height, depth of reach, and angle to accommodate a variety of shapes and sizes of parts.
The MDR can be operated in any open area or be moved inside a paint booth after the paint process has been completed.
The heaters can operate with a variety of power supplies ranging from 120VAC to 480VAC. The racks can be ready to operate in as little as 30 minutes. Fuel choices include natural gas or propane with multiple fitting and mounting options.
Heater racks double production
Automotive Equipment Manufacturer Reduces cure time from 20 to 10 minutes
An Oklahoma manufacturer of pneumatic cylinders, controls, and valves manufacturer for the mobile, truck equipment, and automotive markets had been using a batch convection oven to cure powder coat. The oven was inoperable and would have required a significant investment to repair. An outside powder coating company had taken over the process for the company, charging tens of thousands of dollars per month.
Catalytic Industrial Systems designed and built a gas catalytic Infrared solution that doubled their capacity while bringing the coating process back in house. The solution consisted of two heater rack sections retrofitted into the existing oven enclosure. Factory testing proved that CIS’ Infrared system reduced the cure time from 20 minutes down to 10 minutes. The new system doubled the production rate without adding any additional space requirements.
Projects
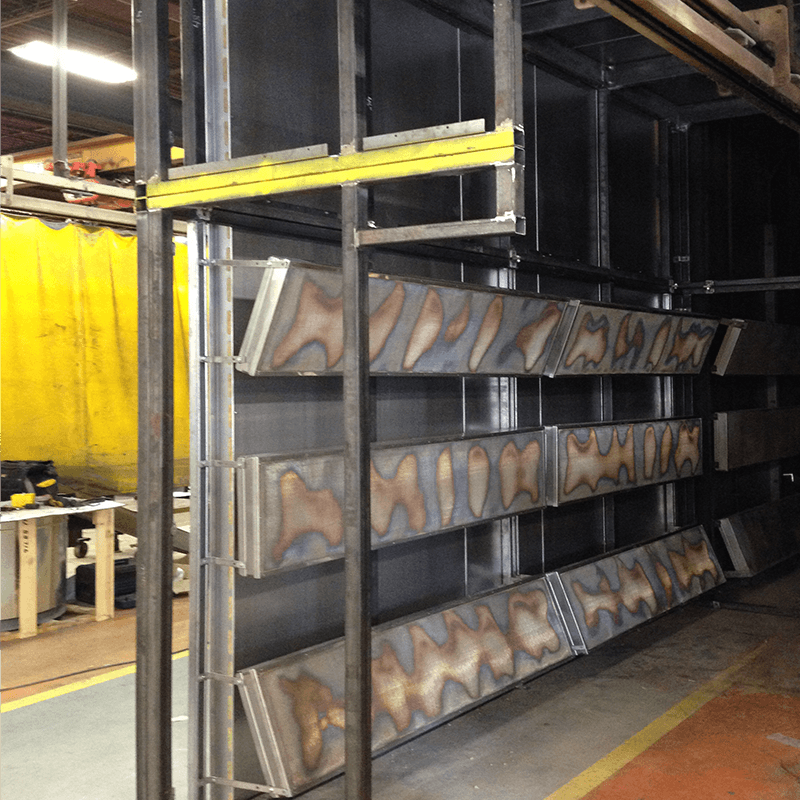
Agricultural Equipment | Paint Curing

Construction & Mining Equipment | Powder Curing
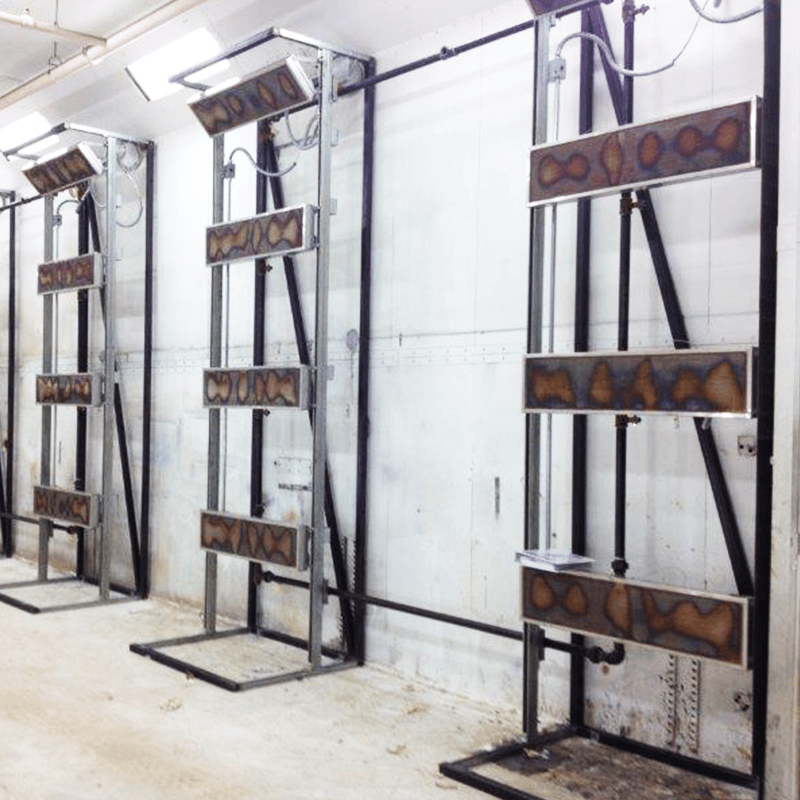
Large Vehicle | Finishing System
OPERATING A CIS CATALYTIC HEATER
CIS catalytic heaters requires electricity and gas to operate. Electric power is required to preheat the heater. During startup, the enclosed electric heating element (E) is turned on for 15 to 20 minutes. Once the catalyst has been preheated, gas can be introduced via the safety valve to begin the catalytic heating process. Gas enters the heater via the dispersion tube assembly (B) and is dispersed by the dispersion screen (C). The gas diffuses through the insulation (D) to come in contact with the catalyst (G) to initiate the catalytic reaction. Infrared energy is emitted and the only byproducts of the catalytic reaction are CO2 and water vapor. The thermocouple is used to control the safety valve or the gas solenoid valve. If the catalyst falls below safe operating temperature, the thermocouple will shut off the gas valve to prevent gas from being emitted.