
powder coating
increase production, Save space & reduce operating costs
CIS gas catalytic ovens are perfectly suited for powder coating applications. Powder Coating is used mainly on metal parts but has gained acceptance for wood products as well in recent years. For a proper finish, the powder coated part may require different multiple heating processes including preheating the part, gelling the powder coat, and curing the coating.
The CIS gas catalytic infrared heating system can be used in any of these steps in place of convection systems with improved performance. For applications with larger or heavier parts, CIS infrared heating systems can be used to improve the performance of an existing convection system.
About Powder coatings
Powder coating is applied as a free-flowing, dry powder. The most common types are Epoxy resin, Polyester, and TGIC powders. The powder may be a thermoplastic or a thermoset. polymer. Manufacturers utilizing powder coating will require an oven to cure the coating.
CIS infrared ovens are ideal for powder coating applications including gelling, whole curing, or used as a booster in combination with a convection oven.
COMBINATION INFRARED/
CONVECTION OVENS
The combination of the technologies delivers enhanced results for powder coaters and facilities that process a variable mix of parts. In a combination oven, the infrared portion of the oven gels, or sets, the powder coating ahead of the convection oven portion. This accelerates the convection soak portion that completes the cure.
The infrared energy used in this ramp-up zone also prevents powder loss by gelling the finish before it can be disturbed by the air turbulence in the convection section. It can also help to prevent cross-contamination in facilities that use more than one color of powder.
powder booster oven
A bank of CIS heaters installed into the front entrance of an existing convection oven, or a complete CIS oven installed outside the existing oven will double or triple production by reducing process time.
Powder Gel oven
This type of oven is used to gel the powder before entering a convection oven to keep the powder from blowing off and reducing the footprint of the oven.
Powder cure oven
In this oven the parts are cured by infrared in a continuous flow or batch style oven.
cis oven cures 2x faster
Automotive Manufacturer improves process & saves $10k per month
Our customer, a manufacturer of automotive parts, had an old convection oven that died. They were spending $10K per month by outsourcing to a local powder coater. Due to an upcoming building move, the company was hesitant to invest in a new oven. The team at CIS devised a short term plan to use the existing oven as a frame by constructing two heaters on racks as subassemblies, The customer purchased two heater rack systems constructed by CIS installed into their broken convection oven frame.
This minimized the initial cost and reduced the cost of moving. Their previous convection system took 20 minutes to cure. The new infrared convection system, at half the length of the old oven, cured the powder in 10 minutes. After they moved to their new location, CIS created a new modular oven system that integrated the rack CIS built first. This led to monthly savings of $10K by bringing the process back in house.
Projects
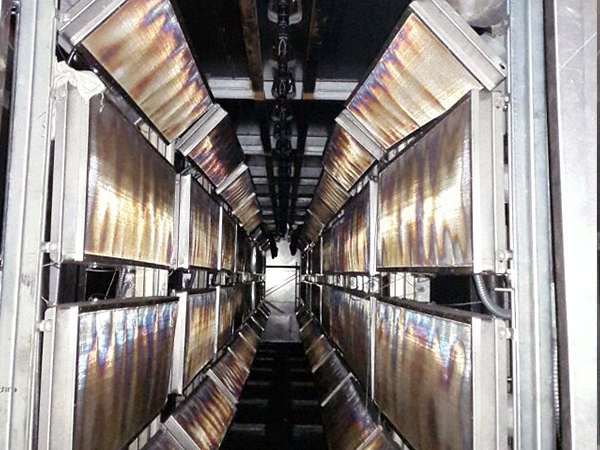
Light Fixtures | Powder Coating

Large Vehicles | Powder Coating

Automotive Engines | Powder Coating

Doors | Epoxy Coating

Automotive Parts | Powder Coating

Propane Tanks | Powder Coating

Steel Bumpers | Powder Coating
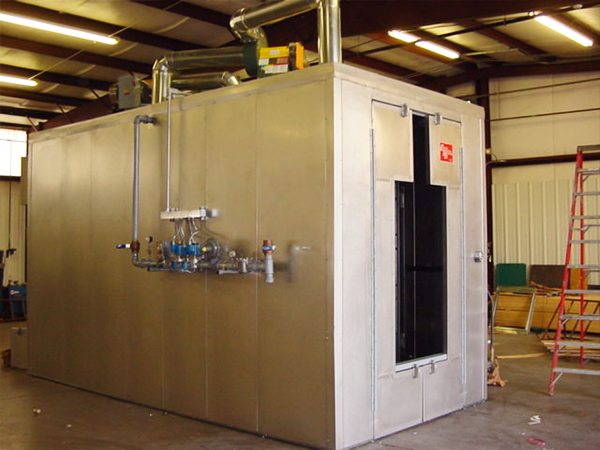
Fuel Tanks | Powder Coating